
Michael Sassano
Founder, Chairman & CEO Somai Pharmaceuticals -Investor, Cannabis, GMP, Pharmaceutical &Herbal Medicine https://www.linkedin.com/in/michaelsassano3/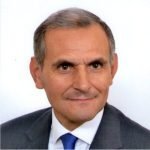
Antonio Guedelha
Production Cycle
Typically, production occurs in several steps and passes through many process equipment rooms. Additionally, one finished product can have several raw materials needed at various times. The Enterprise Resource Planning (ERP) we set up in the previous steps has a Bill of Materials (BOM) — your recipe for the finished product. Standard GMP requirements are for the BOM, and accordingly, the control of the correct BOM in the manufacturing process must always be accurate. Based on this BOM and the quantity of finished product you want to achieve, the ERP should calculate the amount of raw materials necessary to manufacture the product. An important reminder is that the manufacturing process has product losses through many stages. For example, your materials will stick to the equipment from one process to another, so it’s necessary to calculate this slippage. After raw materials arrive at the warehouse, they are analyzed, approved, weighed, and used in manufacturing. This means your systems will be tracking raw materials in the warehouse, weighing room, and production rooms.Stock Needs
The main reason to have a stock of raw materials is to avoid any production stops. All persons who have already worked in a manufacturing facility know the first rule is never stop production. GMP always requires the correct information of the stock by-product and batch number to facilitate running with the most effective stock requirements possible.Stock Management
The goal of stock management is that production never stops, the stock is minimal, and there are minimal losses of raw materials and finished products due to expiration dates. Organization of stock and maximizing your space are essential. As more products are introduced on your lines, the organization of this effort becomes critical. Your ERP will need to be set up to manage such considerations. GMP requires well-defined procedures for stock management to assure the correct batch number is used and prevent the use of expired batch numbers. There are several methods for stock management, and in the same industry, all can be applied or only some.Just in Time
Just in Time “JIT” is used to reduce cash needs to the minimum possible. There is little to no stock, and products are manufactured only when an order comes in. The car industry uses this style which forces the suppliers to carry their stock or fabricate the parts in time for the needs of car production. You can make an agreement with a supplier of a raw material to be supplied in 2-3 days so that the work can be done with almost no stock and the supplier delivers the needed quantities just when you need them. When the supply chains broke during the pandemic, it was primarily due to complex JIT arrangements that could not be filled, cascading the entire system. JIT must be defined and controlled to accomplish all GMP requirements. JIT introduces much pressure on the organization, and there must be procedures in place to avoid skipping steps in the approval and use of these raw materials.ABC Stock Analysis
In this model, most business sales are because the products you manufacture are a small portion of the products you sell in total. This is useful for analyzing the existing stock. You can analyze the stock turnover (value of stock/value of sales) and then make an ABC Analysis to decide which stock you can decrease.Consignment
Sometimes, it is possible to have raw materials in stock that you only pay for when you use them and sell them. This means the stock doesn’t belong to you; It belongs to the supplier. This stock needs to be well controlled since you are responsible for these raw materials that have been consigned.Purchasing
Purchasing the right quantities at the right time requires good planning and tools. There are raw materials sold in a Minimum of Quantity (MOQ); some can take a long time to deliver, and prices are volatile. The time to buy the raw materials depends on the needs that can be ordered or forecasted. It’s normal to work with a forecast for the first four months or longer. This requires the contracts to have precise delivery dates when needed. Remember, GMP will require that you purchase from approved suppliers and have them vetted in advance.Material Requirements Planning
Material Requirements Planning (MRP) is a computer-based stock management process. Forecasting and orders allow the manufacturer to define a production plan for the finished products. Based on the production plan and using BOM, the MRP will calculate the needs of all raw materials and the dates they need to arrive at the facility, with variables factored in such as lead times for supplies, time for receipt, laboratory analysis, and release delays. This takes many inputs and will monitor your purchasing needs for raw materials. Your calculation will help to define reserved batch numbers and quantities. The selection of the batch number will be according to management and the use of stock. GMP will impose the validation of MRP to assure that raw materials planning is not giving instructions to buy quantities of raw materials that are not necessary.Economic Order Quantity
More quantity per purchase order typically means less price for bulking the order. It’s necessary to find the quantity with the lowest price for company needs, best expiration, balance, price, quantity, and stock costs.Minimum Order Quantity (MOQ)
To optimize production, many manufacturers define a MOQ. For example, if you are making batch production in a reactor of 1000 L, you can define the MOQ as the production of a reactor of 1000 L. There are some raw materials that you will need 1 Kg per year, and the MOQ is 20 Kg. If the expiry date is two years, you will use 2 Kg and destroy 18 kg.Lead Time
Suppliers define a lead time. This is the time between the purchase order and the raw material delivery. For finished products, it’s your lead time too. You must write in a contract with a client the lead time. This lead time is calculated based on the lead time of the raw materials, time to manufacture, and some spare time. There is extra time factored in because the manufacturing can’t happen immediately if there are many orders to satisfy.Safety Stock
There are often raw materials or finished products critical to the business that require safety stocking for some products. Safety stock can be defined and managed with the suppliers, so you always have it in stock.FEFO/FIFO
There are several methods to define the order in which to use batches of raw materials. As a joke, some people invented the term First In Still Here or the “FISH” model, meaning that control of the materials was lost. Many GMP Cannabis and Pharmaceutical facilities use First Expire First Out “FEFO.” Others like First In, First Out, or “FIFO” are used for materials without expiry.Stock Levels
The stock levels must be optimized for your business. You can use a financial indicator by dividing the stock value by the average monthly raw materials value used in manufacturing. This value can have figures between 6 to 12 months in cannabis and pharmaceutical industry facilities operating regularly. The stock level needs all your attention to avoid high costs of stock.Stock Costs
If the value of your stock were in the bank, you would be earning interest. This is the cost of your stock. The stock value could be used for investment or to refund loans, among other ways.Controlled Substances
Cannabis is a controlled substance by the Authorities. You need to record all quantities received, where it was used, the losses and reasons for the losses, and the finished product. All these records must be well kept and regularly sent to the Authority. Unjustified differences in the stock may lead to legal consequences. GMP requirements are the key to the proper control of the stock.Regular Inventory Monitoring
By the law, you need to make a regular stock count. This means you will go to your warehouse and count each quantity, each material by batch number, and in some cases, by the container (bag of 25 Kg, drum, other). This means personnel, lift equipment, and weighing balances. The ERP will provide you with a list to make the physical stock count. This list may give the warehouse operator the information on the ERP system’s quantity. You can make a geographic counting, which means you start counting on one side of the warehouse and progress to the other side. In this way, you know all materials were counted. After, you will have to verify the physical quantities against the values in the ERP. The differences must be checked to understand the reason for the change, and afterward, corrections in the ERP must be made. Many companies use the services of an accounting company to follow the inventory and make a report showing it was audited. This report can clarify future questions from the authorities or investors.Dead Stock
Just as it sounds, this is where you lose money. There are three main types: Obsolete inventory consists of goods that lack demand. Imagine if you have a finished product that suddenly the sales decreases or cease; this may result in a complete loss of your goods since they cannot be reused; Damaged goods are items that have become unusable due to mistakes. For example, if you are transporting the product and it falls on the ground, or the box broke because of an impact. Expired goods are items that have reached their expiration date. This is the most difficult to manage, and there will be products to destroy because of expiration dates. Here GMP rules are critical. ERP will follow GMP requirements and help you to avoid significant losses. Your ERP regularly will inform you of products near the expiration date and proceed to use these expiring products first. Defective goods are faulty items, such as due to a production or engineering error. You will produce non-conforming products that will be reprocessed or destroyed.Internet of Things “IoT”
Stock management solves a fundamental business need. A 2017 survey conducted by Wasp Barcode Technologies noted that most small businesses did not track inventory using the current best practices.The survey revealed the following:
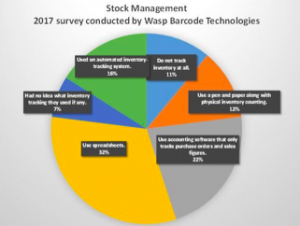