
Michael Sassano
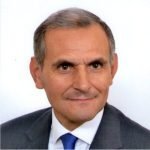
Antonio Guedelha
New Product Basic Data
In order to begin, you will need an analysis of all the possibilities needed to manufacture the product. The following data is preferred:- Pharmaceutical approval of the product and main regulatory documentation
- List of raw materials
- List of API’s
- Manufacturing process main steps and main In Process Control (IPC)
- Analytical Methods
- Definition of the packaging materials
- Forecasts
- Documentation requests